Liquid packaging plays a crucial role in protecting products like beverages, cleaning supplies, and other liquids during storage and transport. Liquid packaging bag technology is a modern and efficient solution for the aseptic filling, transportation, and storage of various liquid and paste-like products.
From selecting the right container to ensuring proper sealing, it’s an essential process for maintaining product quality and safety. This guide will explain what liquid packaging solutions are and why they’re important for businesses across various industries.
What is Liquid Packaging?
Liquid packaging is the specialized process of enclosing liquids—ranging from beverages to cleaning agents—into suitable containers to preserve their integrity, usability, and safety.
Whether it’s water, detergents, or carbonated drinks, liquids require thoughtful handling during packaging to ensure that they remain in optimal condition from the production line to the consumer’s hands.
This process typically includes a variety of steps such as bottle rinsing, filling, capping, and sealing, all of which are performed by a liquid packaging machine. Advanced packaging equipment is crucial in ensuring optimal performance and preventing malfunctions during the packaging process.
Each element of this system must work seamlessly to avoid spills, contamination, or degradation of the product. A well-designed liquid packaging system ensures that these elements are executed with precision, resulting in a complete and efficient packaging solution.
Key Considerations for Liquid Packaging
1. Temperature and Viscosity
Temperature plays a critical role in the liquid packaging process. Not only does it impact the taste and quality of products like beverages, but it also affects the viscosity of the liquid. For instance, colder temperatures can cause certain liquids to thicken, which can impede the filling and sealing processes.
Advanced packaging technologies allow for precise temperature control, ensuring the product’s characteristics remain stable throughout. The viscosity of a liquid—whether thin like water or thick like honey—has a direct effect on the type of machinery used.
Liquids with higher viscosity may require slower filling speeds or specialized nozzles to ensure accurate and consistent dispensing.
2. Container Selection
The choice of container is another key factor in liquid packaging. Containers vary in size, from small one-ounce bottles to massive containers that can hold millions of gallons. The selection of the container depends on both the volume of liquid and the transportation requirements.
Equally important is the packaging material itself. Plastic, glass, and metal each offer distinct advantages and limitations, such as their ability to preserve product freshness or endure transportation without breaking or leaking.
The material and design of the container directly influence how well the liquid product is preserved, protected, and delivered to consumers.
Benefits of Liquid Packaging Solutions
Modern liquid packaging solutions provide a wide array of benefits to manufacturers, not least of which is increased production efficiency. Automation of the packaging process results in faster production cycles, reducing labor costs and improving overall output.
Moreover, these solutions enhance product quality by minimizing human error and providing consistent results with each batch.
Whether handling highly viscous liquids or products with carbonation, liquid packaging systems are designed to accommodate a wide range of liquid properties, further streamlining production.
By automating key steps like capping and sealing, businesses can meet higher demands with improved reliability and precision.
Types of Liquid Packaging Containers
Various materials are available for liquid packaging, each serving specific purposes based on the product being bottled. Plastic, metal, and glass containers are commonly used, each offering different levels of durability and chemical compatibility.
For example, metal containers may be more suitable for chemicals that could degrade plastic, while glass offers an inert barrier ideal for beverages or pharmaceuticals.
Recently, there has been growing interest in liquid pouches, a flexible packaging solution that offers a more environmentally friendly and cost-effective alternative to rigid containers.
Another material, BOPET (biaxially-oriented polyethylene terephthalate) film, is gaining popularity for its high barrier properties, flexibility, and resistance to liquids, making it an ideal choice for specific liquid packaging needs.
Liquid Packaging Solution Options
When it comes to selecting a liquid packaging solution, businesses can choose between fully automated and semi-automated systems.
Fully automated systems, which often incorporate conveyor belts, automatic capping, and sealing, are ideal for high-volume operations, enabling faster throughput and reducing labor requirements.
Semi-automated systems, on the other hand, require some manual intervention, which might suit smaller-scale operations or those looking for a more flexible solution.
The choice of system depends heavily on production volumes, product types, and operational goals. Many businesses partner with contract manufacturers to ensure they are using the most efficient and cost-effective packaging solution for their specific product lines.
Safety and Environmental Considerations
Liquid packaging, particularly for chemicals, presents significant safety and environmental challenges. Physical, health, and environmental hazards must be thoroughly evaluated to protect workers and consumers alike.
Chemical leaks during shipping or storage can lead to contamination, posing risks to both human health and the environment. Strict adherence to Environmental Protection Agency (EPA) regulations is essential, particularly for businesses handling hazardous chemicals.
Modern liquid packaging solutions also emphasize environmental responsibility, seeking to minimize waste and improve the sustainability of materials used in the packaging process.
Liquid Packaging Materials and Design
Liquid packaging materials and design play a crucial role in ensuring the quality, safety, and efficiency of liquid products. The choice of material and design depends on various factors, including the type of liquid, its viscosity, temperature range, and intended use.
When it comes to packaging materials, options like plastic, glass, and metal each offer unique benefits. Plastic containers are lightweight and versatile, making them ideal for a wide range of liquid products. Glass, on the other hand, provides an inert barrier that is perfect for beverages and pharmaceuticals, ensuring that the product remains uncontaminated. Metal containers are often used for industrial chemicals due to their durability and resistance to degradation.
The design of the packaging is equally important. For instance, liquid pouches have gained popularity as a flexible packaging solution that is both environmentally friendly and cost-effective. These pouches are particularly useful for products like soups, sauces, and drinks, offering convenience and ease of use. Bottles and jars, whether made of plastic, glass, or metal, are designed to provide a secure seal, preventing leaks and preserving the product’s integrity.
Temperature range and viscosity are critical considerations in the packaging process. Liquids with varying viscosities, from thin beverages to thick syrups, require different types of filling machinery and packaging materials to ensure accurate and efficient packaging. Additionally, the temperature range at which the product will be stored and transported must be taken into account to prevent any adverse effects on the liquid’s quality.
By carefully selecting the right materials and design, businesses can ensure that their liquid products are safely and efficiently packaged, maintaining their quality from production to store shelves.
Regulatory Compliance and Standards
Liquid packaging is subject to various regulatory requirements and standards, including those related to safety, quality, and environmental sustainability. Adhering to these regulations is essential for ensuring consumer safety and maintaining the integrity of the product.
Regulatory bodies such as the Environmental Protection Agency (EPA) and the Food and Drug Administration (FDA) set stringent guidelines for packaging liquids, particularly those that are hazardous or intended for human consumption. These regulations cover aspects such as material safety, labeling, and the prevention of contamination.
For instance, packaging materials must be tested to ensure they do not react with the liquid product, which could compromise its safety and effectiveness. Additionally, proper labeling is crucial for providing consumers with essential information about the product, including its ingredients, usage instructions, and any potential hazards.
Environmental sustainability is another key consideration in regulatory compliance. Businesses are increasingly required to adopt eco-friendly packaging solutions that minimize waste and reduce the environmental impact. This includes using recyclable materials and designing packaging that is easy to dispose of or repurpose.
Compliance with these standards not only protects consumers but also enhances a company’s reputation and marketability. By prioritizing safety, quality, and sustainability in their packaging processes, businesses can build trust with their customers and contribute to a healthier environment.
In conclusion, understanding and adhering to regulatory requirements and standards is a fundamental aspect of liquid packaging. It ensures that products are safe, high-quality, and environmentally responsible, ultimately benefiting both consumers and businesses.
Choosing the Right Liquid Packaging Solution
Several factors must be weighed when selecting the ideal liquid packaging system. First, businesses must consider the characteristics of their product—whether it’s a viscous cleaning agent, a carbonated beverage, or a temperature-sensitive pharmaceutical.
Next, production volume plays a major role in determining the level of automation needed. Durability, practicality, and suitability for transportation must also be evaluated to ensure that the container will safely deliver the product without damage.
Advances in packaging materials and technology now offer an impressive range of options, enabling businesses to customize their solutions to meet specific operational needs.
Applications of Liquid Packaging
Liquid packaging solutions are widely used across a broad range of industries. In the food and beverage sector, liquid pouches are commonly employed for packaging everything from soups to sauces and drinks.
The pharmaceutical and cosmetics industries also rely heavily on liquid packaging for products such as lotions, serums, and liquid medicines.
Industrial chemicals, cleaning agents, and personal care products often utilize packaging systems tailored to their unique chemical properties, ensuring safe and efficient distribution.
This versatility demonstrates the adaptability of liquid packaging to meet the needs of diverse markets.
Best Practices for Liquid Packaging Operations
To ensure success in liquid packaging operations, attention must be paid to several best practices.
- Proper handling techniques are essential to prevent product damage during the filling, capping, or sealing processes.
- Temperature control remains paramount, especially for products where viscosity plays a significant role in maintaining quality.
- Pressure control is also critical, particularly when packaging carbonated beverages.
- Additionally, allowing for excess volume—commonly referred to as “headspace”—can prevent overflows and ensure that the container seals properly, especially for liquids that may expand or change state under certain conditions.
Conclusion
Liquid packaging is an intricate and vital aspect of the manufacturing process, especially for industries dealing with a wide range of liquid products. By addressing critical factors such as temperature, viscosity, and container material, businesses can ensure their products are safely and efficiently packaged, improving quality while reducing costs.
Advances in packaging technologies offer businesses numerous options, allowing them to find solutions that best suit their needs. Choosing the right packaging partner is essential for ensuring that all these elements work harmoniously to support a successful liquid packaging operation.
Partner with WestPenn for Expert Liquid Packaging Solutions
Looking for a reliable liquid packaging partner? WestPenn offers state-of-the-art packaging solutions tailored to your product’s unique needs, ensuring efficiency, safety, and sustainability. Contact us today to explore how we can optimize your packaging process and enhance your production capabilities.

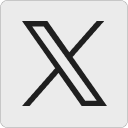