The Oil Blending Process
Blending oil has been a practice for many years. Oil, like motor oil is used to lubricate the internal parts of most engines and that helps to reduce the wear caused by the friction of moving parts. Oil can also clean, improve certain types of seals, cool the engine and keep parts from corrosion. Most motor oils are a combination of petroleum and non-petroleum synthesized chemical compounds. There are many different oils on the market today and those can be made from hydrocarbons, poly-internal olefins and polyalphaolefins ingredients. Getting all of these different types of compounds into one liquid is quite a process. Oil blending is done by many companies with facilities all over the world, including the United States. With most motor oils, they start the blend with a base and start to add the compounds that will make the finished product.
There is a basic blending process that has been used for decades by bunker suppliers. The process is used by the supplier to prepare the blend in a holding tank. Before the company can deliver the product to customers, there are many components added to the tax, mixed and then analyzed by the supplier. Because this process is very long, which adds costs that are passed to the consumer, advancements in technology have been put in place for a technique called in-line blending. Many companies that blend oil, buy a base in bulk for a cheap price and then add they compounds they think will make the best finished product. In the end you have motor oil, for example, and that is why you see so many different types when you head to the store to buy some. Because lower cost heavy crude oil is not as available as it once was, companies blend two different types of oil with hopes of enhancing flexibility and profitability.
In-line blending is just one cost effective alternative and gives companies a better chance to process a wider range of finished oil products. The process that involves blending oil includes many different pieces, just like the compounds that go into it. A good oil blending system consists of flow meters, control valves, mixing, control and analyzer systems. For a company to become successful at blending oil, the in-line blender must perform at a high level of quality once integrated with the blender and the control system. In-line blending is defined as “The controlled proportioning of two or more component streams to produce a final blended product of closely defined quality from the beginning to the end of the batch, thus permitting the product to be used immediately or loaded directly to the customer”.
Batch blending was the way it has been done for years before in-line blending. In-line blending has many different advantages compared to batch blending, including lower labor cost, simplified processing plants, improved quality, reduced waste, simplified planning, lower production costs, increased flexibility of fixed assets and reduced processing time. All of these factors lead to a product that can be produced faster and for less money, thus giving consumers a break at the register. In-line blending can also be supplied in many different configurations including barge units, trailer mounted units or skid-mounted systems. Once you have the configuration in place, the type of blending that you do is actually called ratio blending. The ratio blending system is very dependent on accuracy. That has a lot to do with the flow meters and flow transmitters and how accurate the process is.
When you are blending in-line, the actual mixing of the streams together is critical. The mixing of an in-line blend has to be accurate and done dynamically as the components come together and must be continuous. The in-line blending process almost always has inadequate nature turbulence and that is what helps to blend the product throughout the flow. There are mixing devices that help to combine the streams accurately and consistently throughout the process. One of those devices is called a static mixer element. The elements will divide and turn the fluid, which increases the rate of energy dissipation through pressure loss. The loss that occurs is proportionate to other parts of the process, especially small mixtures. Some companies have moved away from static mixers and use what is called a JetMix mixing system. With a JetMix system, a powered loop is used to produce sufficient energy to blend the components. The JetMix mixing system is useful when an analyzer such as a viscometer is installed in the blend header.
Trimming can be used to help keep an accurate eye on the blending system. A trim set point like viscosity becomes part of the overall blend process and that is used to trim the volumetric ratios. This part of the process can give an increased level of accuracy in the blended product. Great care must be used when applying a trim to a mix or it could have adverse effects on the accuracy of the blending system. Some things that should be considered include, installing the analyzer in the mix section of the blend, keeping the blend system efficient throughout the process, keeping the sunlight away from the analyzer, keeping things like noise or vibration away from the analyzer as well. Selecting the trim stream should be done carefully and only the one with the most effect on the blended product should be used.
Sampling throughout the process is a good way to keep an eye on the quality of the product. A number of international standards are included in the sampling process. The sample can only be the bites and they should be taken from the blend header at flow proportioned intervals. Because flow rates are difficult to maintain throughout the in-line blending process, the “cut back” and “cut up” part of the process combats that problem.
The oil blending process is one of the most accurate and gentle processes for companies that blend crude oil. Each step of the way is monitored for accuracy and without that monitoring there would be a very high error rate. With the advances in technology, the in-line blending system has been a cost saver for companies and consumers alike.

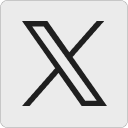