Keeping your liquid packaging safe and of high quality has never been more critical. As a liquid packaging company, we know how important it is to find the proper packaging for liquid products. As consumer preferences and industry regulations change, you need to focus on packaging efficiency and the safety and integrity of your liquid products.
Liquid packaging safety stops contamination and extends shelf life and durability during distribution. Good packaging protects your product and consumer health, meets regulations, and your brand reputation
As consumers become more aware and environmentally conscious, adopting best practices in packaging helps you stay ahead of the game and deliver high-quality products.
Understanding Liquid Packaging Solutions
Your liquid packaging solutions protect products like food, beverages, pharmaceuticals, and chemicals from contamination and spoilage.
These systems handle filling, sealing, labeling, and capping- a clean and efficient process. Your industry may have specific needs, and modern packaging technologies have solutions to meet those requirements.
Liquid packaging solutions can be customized to fit different industries and products. For example, food and beverage companies may require solutions that meet strict safety and hygiene standards, while pharmaceutical companies may require solutions that ensure product integrity.
Businesses can choose the right liquid packaging solution by understanding their industry and products. Investing in flexible packaging allows you to adapt to different product types and customer preferences.
Key Factors in Packaging for Liquid Products
When choosing packaging for your liquid products, consider the following:
- Durability: Your packaging should withstand storage, transportation, and handling without breaking or leaking. Choose materials that are impact-resistant and temperature-tolerant.
- Practicality: Choose designs that are easy to use and fit your product purpose. Consider pouring ease, resealing, and storage convenience.
- Shipping: Your packaging should protect against damage and environmental factors during transit. Lightweight materials reduce shipping costs, and tamper-evident features ensure safety during transportation.
Your product’s characteristics like thickness, acidity, and chemical properties – also affect your packaging choices. Advances in materials and technology give you many options, like multi-layered packaging that provides an extra barrier against contamination and UV protection.
Choosing the Right Packaging Materials
Choosing the right materials is key to keeping your product safe and fresh. Eco-friendly options like recyclable glass and biodegradable pouches are becoming popular. Your choice should fit your product.
There are many liquid packaging materials to choose from: glass, plastic, metal, and paper. Each has advantages and disadvantages, and businesses should consider these when choosing. For example, glass is popular for liquid packaging because it’s non-porous and can be sterilized, but it’s heavy and expensive. Plastic is lightweight and cheap but not suitable for some products.
And consider the recyclability and carbon footprint of your chosen materials to match your sustainability goals. Plant-based plastics and water-soluble films are emerging as viable options that are environmentally responsible.
Ensuring Product Quality and Safety
To maintain quality and safety, consider these factors:
- Prevent Leaks: Check seals and closures regularly to ensure they are secure with no spills and contamination.
- Monitor Cap Torque: Properly tightened caps prevent contamination and leaks, ensuring a secure seal that maintains product integrity.
- Use Resealable Options: Resealable packaging like spouted pouches and screw top caps makes it more convenient and reduces waste by keeping the product fresh.
- Do Regular Inspections: Regular checks help you detect issues before they reach the consumer and ensure compliance with industry standards.
- Implement Tamper Evident Features: Safety features like shrink bands and induction seals give consumers peace of mind and a clear indication of product integrity.
- Material Compatibility: Choose materials that won’t react to your product to avoid degradation and health risks.
- Store Properly: Store your products under the right conditions to prevent spoilage and material degradation.
- Train Your People: Educate your staff on best practices to avoid mistakes and boost consistency in the packaging process.
By following these, you can produce high-quality products, increase customer satisfaction, and minimize losses due to packaging failures.
Ensuring Product Quality and Freshness
Product quality and freshness are top priorities for businesses that package liquids. This means implementing good manufacturing practices (GMPs) and using high-quality packaging materials and equipment. Businesses should also consider the filling machine, production line, and storage conditions to ensure products stay fresh and safe throughout the supply chain.
One way to have product quality and freshness is to use aseptic packaging, filling and sealing containers in a sterile environment. This is used for dairy products, juices, and other beverages.
Another way to have product quality and freshness is to use modified atmosphere packaging (MAP), replacing the air in the container with a gas like nitrogen or carbon dioxide. This is used for snacks, baked goods, and other food products.
Benefits of Automated Liquid Packaging Systems
Automated systems can help you a lot. Automation makes your operations more efficient by streamlining packaging, allowing you to meet high demand and maintain product consistency.
It saves you time by reducing manual labor, allowing your employees to focus on other tasks, and lowering the risk of mistakes.
It also helps you save costs by reducing the need for a big workforce and optimizing resource use, making you more profitable. Plus, automation allows better tracking and quality control through integrated software monitoring real-time production.
Automated systems ensure better quality control by providing precise filling, capping, and sealing processes, producing consistent, high-quality products.
With advanced conveyor belts and sealing mechanisms, your packaging will be hygienic and uniform. Even semi-automated systems can significantly improve manual processes and are cheaper for small to medium businesses.
Meeting Consumer Demands and Expectations
Today’s consumers want packaging that’s practical and visually appealing. A good design can influence buying decisions and build brand loyalty. You should focus more on bold designs, clear labeling, and ergonomic packaging to attract and retain customers.
Convenience is another major factor. Easy to open, resealable, and portable packaging fits busy lifestyles and makes your products more appealing. Consider using smart packaging technology like QR codes for product tracking and usage instructions.
Sustainability is more important than ever. Many consumers prefer packaging that’s recyclable, biodegradable, or made from eco-friendly materials. Offering refillable packaging or packaging with minimal waste can boost your brand reputation.
Transparency is key to building trust. Clearly displaying ingredients, usage instructions, and expiration dates allows customers to make informed decisions and builds brand credibility.
Personalization is getting popular. Features like QR codes that provide additional information or promotions can increase engagement and add value. Smart packaging technology like freshness indicators or temperature-sensitive labels can further boost customer satisfaction.
Packaging Regulations and Compliance
Regulatory compliance and safety are part of liquid packaging operations. Businesses must comply with various packaging regulations and standards, including food safety, environmental protection, and worker safety.
In the food and pharmaceutical industry, your packaging must have tamper-evident features to reassure consumers. Stay updated with regulatory changes to avoid legal issues
Good manufacturing practices (GMP) and regular audits will help you to maintain compliance and quality standards. By complying with these regulations, you can ensure that your products are safe for consumers and that your operation is environmentally sustainable.
One way to ensure regulatory compliance and safety is to implement a quality management system (QMS) that includes procedures for monitoring and controlling the packaging process. Also, investing in compliance-focused packaging software can simplify your record-keeping and audits.
Business should also train their employees on safe handling and packaging of liquids. Businesses can also regularly inspect their packaging equipment and facilities to ensure they are in good condition and meet regulatory requirements.
Liquid Packaging Best Practices
To get the best results:
- Assess Product Characteristics: Know your product’s thickness and light sensitivity.
- Choose the Right Packaging: Select material that provides protection and aligns with your sustainability goal.
- Implement Quality Control: Set up processes to ensure packaging consistency and safety.
- Regular Inspections: Check frequently for any signs of damage or leakage to catch issues early.
By following these best practices, you can keep your products fresh and safe for your customers.
Elevate Your Packaging with West Penn Oil
Want to improve your liquid packaging process? Our expert solutions at West Penn Oil are designed to meet your unique needs, keeping your products safe and fresh. Contact us today to see how we can help you achieve packaging excellence!

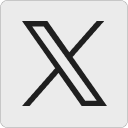