Selecting the right liquid packaging material is a critical component of business success for any company dealing with liquid products. From beverages to industrial chemicals, packaging affects not only the shelf life and safety of your product but also your brand’s reputation and environmental impact.
In this guide, we’ll walk you through the essentials of choosing the best liquid packaging materials, highlighting key factors to consider and breaking down the pros and cons of different solutions.Whether you’re launching a new product or reevaluating your current packaging strategy, this guide will help you make informed, sustainable decisions.
Understanding Your Packaging Needs
Before diving into packaging materials, it’s essential to first identify your product’s specific requirements. Every product has unique qualities that dictate its packaging solution.
For instance, beverages require packaging that preserves freshness, while industrial liquids might demand containers resistant to chemical reactions. Learn about some safety precautions with different types of petroleum containers.
The target market also plays a significant role—whether you cater to high-end customers who expect premium, durable packaging or budget-conscious buyers prioritizing convenience.
Considering shelf life is paramount. For perishable goods, the right packaging can mean the difference between a product that lasts weeks versus months.
Product packaging plays a crucial role in branding and consumer connection. It must be durable, suitable for shipping, and meet the specific needs of liquid products. Advancements in packaging solutions and materials, along with expert guidance, can help businesses choose the most effective options for their product packaging.
Ultimately, product quality, longevity, and customer satisfaction hinge on your packaging choice. The packaging is often the first physical interaction a customer has with your brand, making it a critical aspect of your product’s overall appeal.
Types of Liquid Packaging Solutions
There are two primary categories of liquid packaging solutions: rigid and flexible packaging. Each has distinct advantages and considerations. A streamlined packaging process is crucial for improving operational efficiency, maintaining product quality, and meeting the evolving demands of customers in a competitive market.
Rigid Packaging
- Durable and provides excellent protection.
- Commonly used for high-value or fragile liquids, like perfumes or premium beverages.
- Includes glass bottles, plastic containers, and metal cans.
- Metal packaging offers advantages such as durability and excellent protection but has disadvantages like chemical reactivity and corrosion, impacting the environment. It is commonly used in industrial and metal cleaning sectors.
- Heavier, bulkier, and may increase transportation costs.
- Often reusable or recyclable, contributing to sustainability.
Flexible Packaging
- Lightweight, adaptable, and space-saving
- Ideal for compact, portable products like juices, sauces, or cleaning liquids
- Includes stand-up pouches, spouted pouches, and sachets
- Less protective compared to rigid packaging
- Reduces shipping costs and environmental impact by using less material
Evaluating Packaging Materials
The material you choose for your packaging will largely define its performance and environmental impact. Common materials include plastic, metal, and glass.
Plastic is versatile and cost-effective but raises sustainability concerns due to its non-biodegradable nature. Metal, often used in industrial liquid packaging, provides durability and excellent chemical resistance, though it can be costly. Glass, a traditional favorite for premium beverages or cosmetics, offers an inert barrier to protect liquids, but its fragility and weight are downsides.
Chemical compatibility is critical, especially for industrial liquids or consumables. Some liquids may react with certain plastics, leading to contamination. In contrast, glass and metal provide more inert solutions. However, metal packaging, while durable and resistant to chemicals, can suffer from corrosion and has a significant environmental impact due to its chemical reactivity.
It’s essential to consider the environmental footprint of each material—glass and metal can be recycled, but at a higher energy cost, while some biodegradable plastics offer a more sustainable alternative.
Key Considerations for Packaging Solution
- Size and Shape: The dimensions of your packaging must suit your product’s needs while being practical for storage and transportation.
- Filling, Capping, and Labeling: Ensure the packaging supports efficient processing, from filling to sealing.
- Cost and Efficiency: Consider the long-term cost savings of choosing the right packaging solution, including reduced waste and faster processing times.
Packaging Equipment and Machinery
Choosing the right equipment is crucial for maximizing productivity. Consider the production volume: smaller businesses may benefit from semi-automated systems, while large-scale operations will need fully automated machinery for higher output.
The type of material and container shape also influences the machinery you choose. Some equipment specializes in filling flexible pouches, while others are tailored for rigid containers.
Quality and reliability should not be overlooked. A machine breakdown can lead to costly delays, so opting for equipment with a proven track record of performance is essential.
Pouches for Liquid Packaging
Pouches have surged in popularity, especially for products such as juice, sauces, and cleaning liquids. They offer convenience for both the manufacturer and the consumer. For manufacturers, pouches can lower shipping costs due to their lightweight nature. For consumers, stand-up pouches with spouts offer ease of use and portability.
There are different types of pouches to consider. Stand-up pouches with spouts are ideal for single-serving products, while dual-component liquid pouches can store separate ingredients until mixing is required. The seal type and opacity also matter, depending on the product’s sensitivity to light and air.
Bulk Packaging Considerations
Bulk packaging solutions are ideal for industries that deal with large quantities of liquids, such as chemicals or oils. Packaging options include metal drums, tank trucks, and bulk rail containers. Bulk packaging provides significant cost savings and reduces waste.
However, you need to ensure that the packaging material can withstand the liquid’s weight and chemical properties. Also, consider how bulk packaging integrates into your supply chain. Containers need to be easily handled by your production and distribution processes without causing delays or damage.
Compliance and Safety
In an era of stringent regulations, compliance is a non-negotiable factor. Your packaging solution must adhere to industry-specific standards. For example, food-grade liquids must comply with health regulations, while chemicals require specific hazard labels and safety features.
Safety is also paramount during packaging and transportation. Choose materials and equipment that minimize risk, whether it’s for product preservation or employee safety during handling. These EPA regulations will help you stay up to date with some of the legal liquid packaging requirements.
Sustainability and Environmental Impact
Sustainability is no longer a trend—it’s a business imperative. Packaging that reduces waste and promotes recyclability is increasingly favored by both consumers and regulatory bodies. Biodegradable materials are an excellent choice for reducing environmental impact, though they might come at a higher cost.
Long-term, sustainable packaging can enhance brand reputation, attract eco-conscious consumers, and even offer cost savings by reducing waste and improving material efficiency.
Innovations in Liquid Packaging
The liquid packaging industry is constantly evolving, with new innovations and technologies emerging to improve efficiency, sustainability, and product quality. Staying ahead of these trends can give your business a competitive edge. Here are some of the latest innovations in liquid packaging:
- Advanced Packaging Materials: The development of new materials such as bioplastics, nanomaterials, and graphene-based materials is revolutionizing the industry. These materials offer enhanced sustainability and performance, providing better protection for liquid products while reducing environmental impact.
- Smart Packaging: Technologies like RFID, NFC, and QR codes are being integrated into liquid packaging to enhance product tracking, authentication, and consumer engagement. Smart packaging can provide real-time information about the product, improve supply chain transparency, and offer interactive experiences for consumers.
- Active Packaging: Active packaging technologies, including oxygen scavengers, ethylene absorbers, and antimicrobial agents, are being used to extend the shelf life of liquid products and improve their quality. These innovations help maintain product freshness and safety, ensuring a longer shelf life and better customer satisfaction.
- Sustainable Packaging: The push for sustainable packaging solutions is stronger than ever. Refillable containers, biodegradable packaging, and recyclable materials are being developed to reduce the environmental impact of liquid packaging. These solutions not only appeal to eco-conscious consumers but also help businesses meet regulatory requirements and improve their sustainability credentials.
By embracing these innovations, businesses can enhance their packaging solutions, improve product quality, and reduce their environmental footprint.
Cost Analysis and Budgeting for Packaging
When it comes to packaging liquids, cost is a critical factor to consider. The cost of packaging can vary widely depending on the type of packaging material, the size and shape of the container, and the production volume. Conducting a thorough cost analysis and budgeting for packaging is essential for making informed decisions. Here are some key factors to consider:
- Material Costs: The cost of packaging materials such as plastic, glass, or metal can vary significantly. High-quality materials may offer better protection and sustainability but can also be more expensive. Balancing material quality with cost is crucial for optimizing your packaging budget.
- Production Costs: The cost of producing packaging containers depends on production volume, equipment, and labor costs. High-volume production can lead to economies of scale, reducing per-unit costs. Investing in efficient production equipment can also lower long-term expenses.
- Transportation Costs: The cost of transporting packaging containers is influenced by distance, mode of transportation, and fuel costs. Lightweight and compact packaging solutions can reduce transportation expenses, making them a cost-effective choice for businesses.
- Storage Costs: Storing packaging containers requires space, equipment, and labor. Efficient storage solutions and inventory management can help minimize these costs. Consider the storage requirements of different packaging materials and choose options that optimize space and reduce handling expenses.
By carefully analyzing these factors, businesses can develop a cost-effective packaging strategy that meets their needs without compromising on quality or sustainability.
Consumer Preferences and Market Trends
Consumer preferences and market trends play a significant role in shaping the liquid packaging industry. Understanding these trends can help businesses align their packaging strategies with market demands. Here are some current trends and preferences:
- Sustainability: Consumers are increasingly demanding sustainable packaging solutions that minimize environmental impact. Packaging materials that are recyclable, biodegradable, or made from renewable resources are gaining popularity. Businesses that prioritize sustainable packaging can attract eco-conscious consumers and enhance their brand reputation.
- Convenience: Modern consumers seek packaging solutions that are convenient, easy to use, and portable. Features like resealable closures, ergonomic designs, and single-serve options are highly valued. Packaging that offers convenience can improve customer satisfaction and drive repeat purchases.
- Quality: High-quality packaging that preserves the freshness and integrity of the product is essential. Consumers expect packaging to protect the product from contamination, spoilage, and damage. Investing in quality packaging materials and technologies can enhance product quality and customer trust.
- Design: Visually appealing and innovative packaging designs can capture consumer attention and stand out on store shelves. Creative designs that reflect the brand’s identity and values can enhance brand recognition and appeal.
- E-commerce: The rise of e-commerce has led to an increased demand for packaging solutions designed for online shopping and delivery. Packaging that is durable, tamper-evident, and optimized for shipping can improve the customer experience and reduce return rates.
By staying attuned to these consumer preferences and market trends, businesses can develop packaging solutions that meet customer expectations and drive market success.
These new sections should seamlessly integrate into the existing article, providing valuable insights and practical advice for businesses looking to optimize their liquid packaging strategies.
Selecting the Right Packaging Material
Ultimately, selecting the best packaging material comes down to balancing your business needs, product quality, and customer satisfaction. Whether you prioritize cost, sustainability, or product protection, evaluate each material’s strengths and weaknesses carefully.
Choosing the right material impacts everything from shelf life to customer perception. Durability, cost-effectiveness, and environmental friendliness should all factor into your final decision.
Conclusion
The right liquid packaging can elevate your business, safeguarding product quality while enhancing brand appeal. By understanding your packaging needs, evaluating material options, and considering key factors like sustainability and compliance, you can find the perfect solution. Prioritize a balance between function and environmental responsibility to ensure long-term success for both your product and brand.

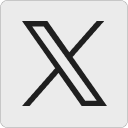